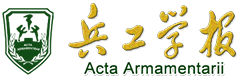
-
Sponsored by: China Association for Science and Technology (CAST)
Editor-In-Chief: Xu Yida
ISSN 1000-1093
-
Hosted By: China Ordnance Society
Published By: Acta Armamentarii
CN 11-2176/TJ
A Numerical Solution of Coupler Curve and Orientation for Reconfigurable Single-driven 3-RRR Planar Parallel Mechanism
LI Xiang;LI Ruiqin;LI Hui;NING Fengping
Sponsored by: China Association for Science and Technology (CAST)
Editor-In-Chief: Xu Yida
ISSN 1000-1093
Hosted By: China Ordnance Society
Published By: Acta Armamentarii
CN 11-2176/TJ
A Numerical Solution of Coupler Curve and Orientation for Reconfigurable Single-driven 3-RRR Planar Parallel Mechanism
{{custom_ref.label}} |
{{custom_citation.content}}
{{custom_citation.annotation}}
|
/
〈 |
|
〉 |