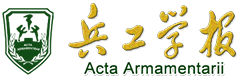
-
Sponsored by: China Association for Science and Technology (CAST)
Editor-In-Chief: Xu Yida
ISSN 1000-1093
-
Hosted By: China Ordnance Society
Published By: Acta Armamentarii
CN 11-2176/TJ
Simulation Study of Bearing Band Engraving Process and Interior Ballistic Process Based on Thermo-mechanical Coupling FEA Model
DING Chuan-jun;ZHANG Xiang-yan
Sponsored by: China Association for Science and Technology (CAST)
Editor-In-Chief: Xu Yida
ISSN 1000-1093
Hosted By: China Ordnance Society
Published By: Acta Armamentarii
CN 11-2176/TJ
Simulation Study of Bearing Band Engraving Process and Interior Ballistic Process Based on Thermo-mechanical Coupling FEA Model
ordnance science and technology / bearing band engraving / thermo-mechanical coupling / extracting bullet force / finite element method {{custom_keyword}} /
Collection(s)
/
〈 |
|
〉 |