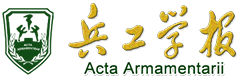
-
Sponsored by: China Association for Science and Technology (CAST)
Editor-In-Chief: Xu Yida
ISSN 1000-1093
-
Hosted By: China Ordnance Society
Published By: Acta Armamentarii
CN 11-2176/TJ
Analysis and Prediction of Surface Topographyin Peripheral Milling Based on Workpiece Vibration and Milling-Tool Structure
LIU Yang;QIN Guohua;WU Zhuxi;LOU Weida;LAI Xiaochun
Sponsored by: China Association for Science and Technology (CAST)
Editor-In-Chief: Xu Yida
ISSN 1000-1093
Hosted By: China Ordnance Society
Published By: Acta Armamentarii
CN 11-2176/TJ
Analysis and Prediction of Surface Topographyin Peripheral Milling Based on Workpiece Vibration and Milling-Tool Structure
{{custom_ref.label}} |
{{custom_citation.content}}
{{custom_citation.annotation}}
|
/
〈 |
|
〉 |